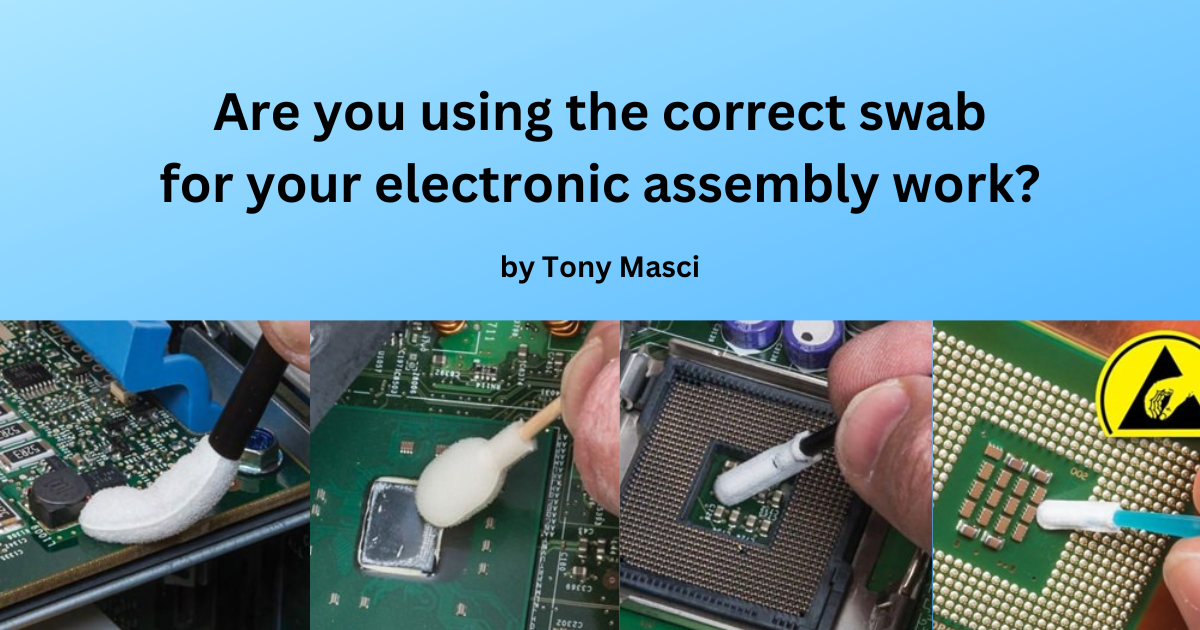
Swabs have come a long way since the simple cotton swab on a wood stick was the norm. And while cotton swabs have their uses, more complex solutions are needed for critical industries like laboratories, medical device assembly, cleanrooms, electronic manufacturing, PCB assembly, and rework and repair.
Swabs are useful precision tools for technicians and operators to perform delicate and meticulous tasks like precision cleaning, repair, and assembly.
Types of Swabs
There are many materials used to make swab heads but let’s discuss the most common materials found in the precision cleaning environment. Cotton is very absorbent and, in many cases, a good cleaning choice. Cotton is tolerant of cleaning solvents, however, irregularities from being a naturally derived material limit their usefulness since they can often shed fibers. Next, polyurethane foams are absorbent and generally clean, they tolerate the most frequently used cleaning solvents such as isopropyl alcohol, however, more aggressive cleaning solvents such as acetone will weaken the foam structure and they will shed particles. Polyester is an especially useful and popular material to make cleanroom swabs. Polyester is engineered clean from the beginning, and it is very tolerant of almost all cleaning solvents. Static dissipative swabs should be used when working with delicate microcircuits. The risk of ESD damage can be reduced by using a swab with a static dissipative handle. Wrapped swabs generate fewer particles as the wrapped form encapsulates cut edges. They are hand-made so they are usually more expensive than machine-made swabs.
Let's recap the common swabs that are used in critical applications. Remember that some swabs may be hybrid swabs, such as foam swabs with cotton interiors or wrapped polyester swabs.
Cotton Swabs
- Most common swab
- Has moderate absorbency, is soft, and low cost
- Broadly used for personal hygiene, DNA testing or cell collection, and in fields from medical to law enforcement
- Ideal for one-time use
- Leaves behind fibers
- Not as strong or durable as other swabs
Foam Swabs
There are two subtypes of Foam Swabs, with distinctions relevant to your selection.
Open Cell Polyurethane Swabs
- Super absorbent
- An upgrade from cotton due to cleanliness and toughness
- Economical
- Ideal when used with alcohol
- Does not leave behind fibers
- Not ideal for scrubbing with harsh solvents like toluene and ketones
- Can tolerate harsh solvents only for a brief time period
Closed Cell Polyurethane Swabs
- Not as absorbent as open-cell polyurethane swabs
- Stronger than Open Cell Polyurethane Swabs
- Resistant to tearing and abrasion
- Does not leave behind fibers
Knitted (woven) Polyester Swabs
- Resistant to many solvent chemicals
- Superior scrubbing ability
- Best for sampling due to great absorption and release ability
- Naturally lowest in NVR (non-volatile residue)
Electro-Static Dissipative Swabs
- Tips can be made out of foam or cotton
- Protects delicate microcircuits from static discharge damage which can destroy or weaken sensitive microcircuits
- Dissipates existing static and prevents static build-up in use
- Usually more expensive than non-ESD swabs
- Only blue handles are completely chemically resistant
Wrapped Swabs
- Tips can be made of cotton, foam, or polyester
- Has no sealed edges, so no risk of scratching delicate substrates
- Generates fewer particles as the wrapped form encapsulates cut edges
- Has high and low areas, the high spots wipe the surface like a squeegee and the low spots collect the soils
- High capacity relative to a fine point for applying lubricants or other liquids, which wick to the tip
- Hand-made so they are usually more expensive than machine-made swabs
Swabs can be used for very specific jobs, but generally, they are used for precision cleaning and contamination removal or application of critical fluids including lubricants, adhesives, and coatings.
Using swabs to clean and remove contamination:
Used for removing contamination and soils from delicate or precision parts, swabs are an effective tool for three reasons:
(1) They can clean a small area as opposed to exposing the whole device to cleaning solvents.
(2) Swabs are good at applying gentle scrubbing action.
(3) Swabs are good at getting into tight little crevices and places where other cleaning devices cannot.
In choosing a swab you must match the cleaning job requirements with the materials and geometries of the swab, essentially using the right tool for the job. First, identify the substrate which will narrow down the type of swab that you need. Plus, it helps limit the type of solvents that are available for your application. Next, identify the soil that you are cleaning. Is it easy contamination such as dust, particulates, and light oils, or is it more difficult soils such as greases, fluxes, adhesives, waxes, and coatings? Then decide if a cleaning solvent is necessary.
Finally, select the swab. For gentle cleaning with nothing or a mild solvent, use any swab. Choose foam for low cost, quick single use, softness, and conformity to a surface. Choose polyester for the highest cleanliness and the highest strength. For aggressive cleaning with a solvent, consider a stronger swab like polyester. If you are working on sensitive electronics, you need to consider static dissipative swab handles.
Using Swabs as an Applicator:
Material compatibility is the most important property to consider when selecting a swab for application purposes. Both the swab head and the handle must tolerate the chemical or fluid being applied.
Adhesives, coatings, and lubricants are often applied with a carrier solvent which can degrade the swab, depositing it on the application affecting both the performance and appearance. Polyester swab heads, which are the most chemically resistant, are likely the best choice.
Swab size, shape, and geometry are other critical properties. Small, pointed swabs are good for applying precise drops of fluid to isolated or narrow locations. However, if the task is applying fluid over a larger area, larger swabs with high fluid capacity are a better choice.
Constantly rewetting a low-capacity swab can be time-consuming and tedious, and may cross-contaminate the fluid reservoir.
Concerns with cross-contamination encourage single-use swabs. Wrapped swabs are especially well suited for precision lubricant application due to their wicking ability. The foam strips or polyester strips create channels that direct a consistent amount of fluid to the point. They are good at balancing the capacity of a larger swab with the precision of a small, pointed swab. They are advantageous for mini-mechanical assemblies such as ball bearings.
(1) Identify the chemical fluid being applied and how it will affect the swab head and handle.
(2) Select a swab material that is chemically compatible with the fluid. Does the fluid contain an aggressive solvent carrier? If so, polyester swab heads are typically the most chemically resistant. However impervious materials like PVDF (polyvinylidene fluoride) are also available. Such swabs can be used once or continuously depending on any concerns for possible cross-contamination.
(3) Select a swab with the proper shape and capacity that matches the task at hand.
(4) Identify the static sensitivity of the substrate. If you are working on sensitive electronics, consider static dissipative swab handles.
SMT Supplies carries an extensive variety of swabs by leading manufacturers such as Chemtronics (Coventry), Easy Braid and Techspray. See our selection here. Our experts can answer your questions regarding choosing the correct swab for your application.