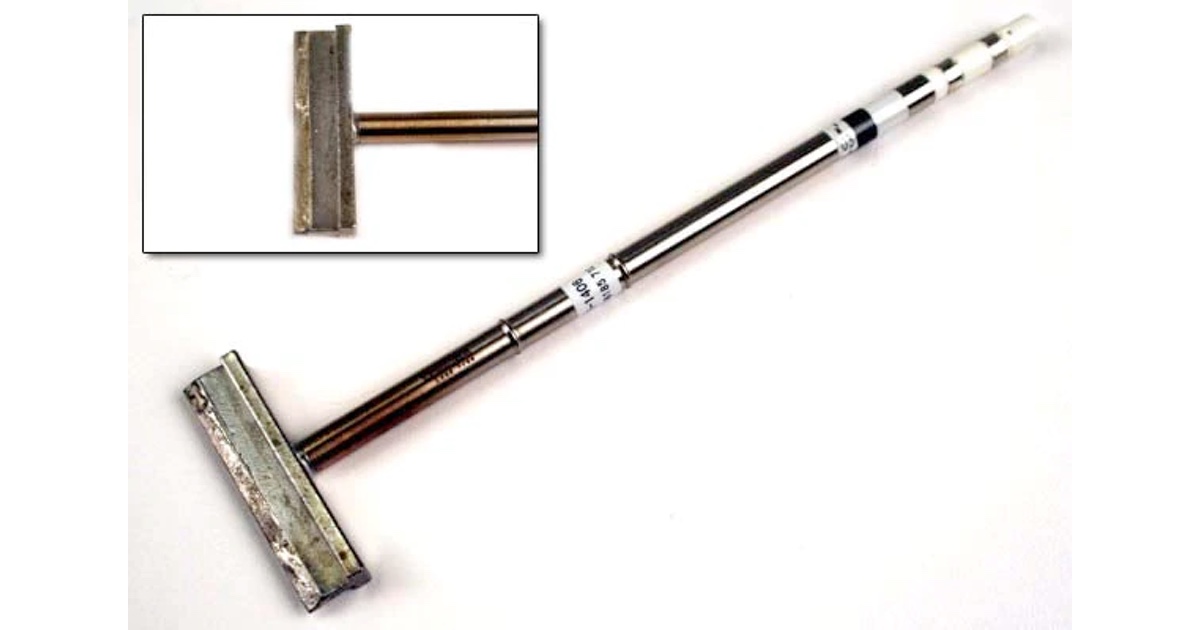
There have been many great articles, whitepapers, blogs, etc. written about choosing the correct solder tip. Kudos to all the authors! I have no desire to repeat their excellent work.
So, why another one? Simple… none to my knowledge have been written by someone with my vast practical experience of watching, teaching, and soldering in all types of environments globally. My own personal soldering experience started in 1979 while working for an OEM in Chatsworth, California, soldering LEDs for spaceflight under a microscope. I was then fortunate during my time at Metcal to see firsthand soldering techniques from operators in Eastern and Western Europe, Southeast Asia, Mainland China, Japan, Korea and South and North America. I also represented Hakko in Southern California for 8 years doing demonstrations and providing training on solder tip care.
With that experience, I have learned that there are generally 4 practical keys to both successfully creating a proper inter metallic connection layer and having a properly working soldering iron on the bench.
Tip Geometry
For the Electronic Manufacturing Services (EMS) provider, speed is of the essence! However, soldering operators working at contract manufacturers won’t typically take advantage of changing the tip to the proper geometry (shape) to meet the demand, so they will utilize just a few tip shapes for all, or most of their soldering work. Though not recommended, they really become experts at making a few tip geometries work all of the time, but the best practice is always to match the tip size to the pad on the PCB. Most soldering equipment manufacturers allow an easy change-out for the tips.
Speed
Again, the EMS Provider is focused on getting the work done fast without damaging the PCB. Like I mentioned above, the trained, experienced EMS operators understand this conflict and can work fast while still producing a proper solder joint. But the challenge that our industry faces is finding good soldering operators. And they will become increasingly difficult to find as our younger generations just don’t want to be soldering 8 hours a day.
Temperature
On average most soldering station temperatures are set way too high. Why? Part of it is due to the myth that the higher the temperature, the faster a solid joint can be made. The other is tip wear (see below). The irony is that speed has a price! Both of these conditions will likely create less tip “life” and higher running consumable tip costs.
Tip Wear
If there is one major complaint by owners and managers of production companies, it is tip life! On the flip side, I continuously hear operators complaining about the tip not heating or working properly. What most fail to realize is that this is very much contingent upon the behaviors of their soldering technicians. More so today than ever with the increase and ubiquitous use of lead-free solder materials, the life of a solder tip can be controlled to a large degree by the operator (with the one exception I noted above: speed). It is my experience that very few soldering personnel take the time to properly maintain their soldering tips! It is so very easy… what I’ve been teaching for years is to simply “tin” the solder tip before your breaktimes, lunchtime and leaving your shift. Tin is the process of flooding the working-end of the solder tip with solder. Make it look ugly! Then put it back in its cradle and turn the station off. No more, no less! By performing this simple behavior day in and day out not only will the soldering operator have a good performing tip, but the tip life will increase! In some cases, it will double.