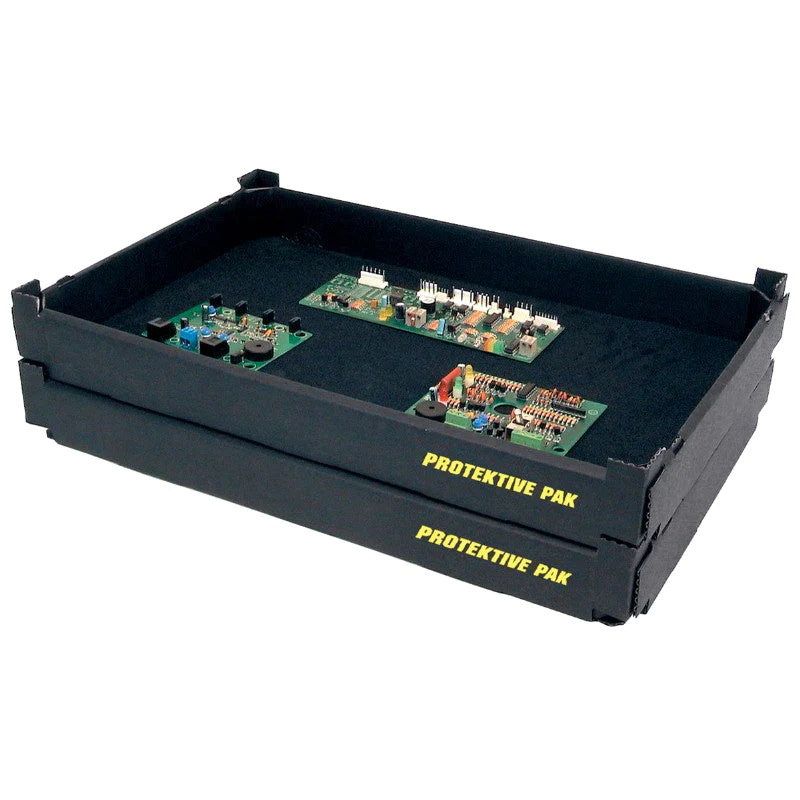
The Customer’s Challenge
A local military and aerospace manufacturer was challenged with finding an ESD tray to meet specific requirements to handle their components from receiving/storage to production. Their Manager of Logistics and Inventory Control was responsible for organizing the BOM for their customers as they received parts to store in the warehouse and move to the floor. They needed a way to receive, organize, and move ESD sensitive components from inventory to production.
The customer was receiving these components in ESD bags; during the kitting process, they were placing the components in ESD safe bins/totes, but the components were unorganized. This caused misclassification of parts and inaccurate inventory. The process limited efficiency and productivity and caused frustration for the customer.
They needed a clear way to separate their stored components into different trays to make sure their components were classified correctly and their inventory was accurate. They also needed this to be done quickly, as their current process was not only causing frustration, but also potential damage to the ESD sensitive components.
SMT Supplies’ Solution
SMT Supplies was ready to take on this challenge. Tony Masci, our Co-owner and General Manager, began working with our supplier Protektive Pak to come up with a solution for this customer. The project quickly evolved into a custom ESD tray because of the narrow parameters requested and because of the strict outer dimension. It also became evident that two trays would be required to achieve the required 48 cavities which would also need an ESD lid.
Protektive Pak provided a drawing and quote including Non-Recurring Engineering (NRE) charges due to the complexity of the aluminum die for all dimensions and number sequencing. Tony coordinated with the customer’s Quality and Production Managers and the local Protektive Pak Representative to quickly receive drawing sign-off so that the 1st Article could be made to meet the time frame.
The Results
Within two weeks, the 1st Article was approved and manufacturing of 100 total ESD trays were completed and delivered to the customer under the initial time and budget request. In total, SMT Supplies was able to provide a custom solution for the customer in two months, from the first question to final delivery of the order.
Once the customer had the final product in hand, they saw their yields improve. Their process was much stronger, their inventory levels were clear, and the ESD sensitive components were being received, stored, and moved to production without damage, which allowed the customer to increase their efficiency and productivity.
Would you like to learn more about how a custom ESD solution can help you? Contact us to start the conversation.