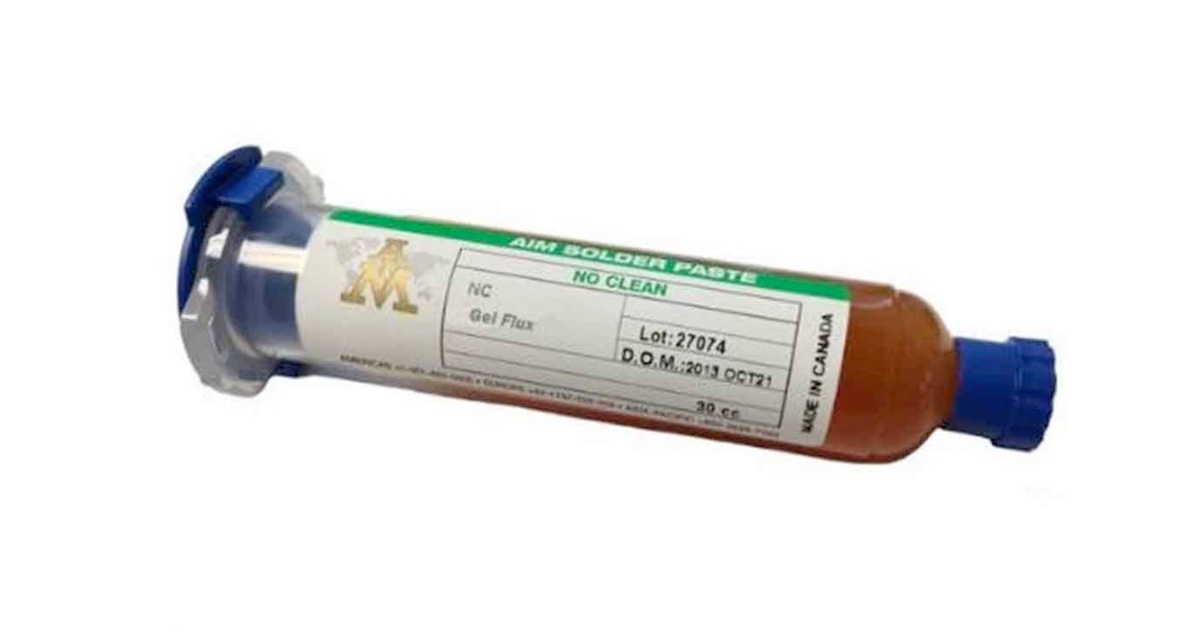
Liquid or Paste Flux for Rework… Which One is Best?
Rework and Repair, the bane of any printed circuit board manufacturing facility. For years we’ve been told that this activity will go away with the advent of surface mount equipment technology improvement, but whether for better or worse, it continues to be an important if not critical element in the overall process.
In this post, we focus on the types of flux recommended for rework. Ideally, no external flux should be used – only the core in the wire. However, external flux not only adds additional activator, but it also serves as a thermal bridge between the soldering iron tip and the workpiece. This makes soldering easier and faster in a manual operation.
Historically, liquid fluxes were not formulated for rework, but we see all types of liquid flux being used today and causing nightmare stories. Whether it’s the wrong flux sneaking into the operation, under processed flux remaining on the board, or improper flux residue removal, they all risk the same fate: field failure! Many process and failure analysis engineers report that most hand solder-related issues are reworked solder joints, and the lion’s share of those are due to the rework chemistry.
Even the right fluxes can cause reliability problems if not processed properly, and by that we mean adequate heat exposure and/or post-soldering cleaning (which we will discuss in a future post). For instance, no-clean fluxes require heat to activate them and if processed properly, they typically pose no threat and can remain on the PCB for the life of the product. But if they don’t see enough heat, dangerous levels of ionic materials may remain and with the simple additions of a voltage bias and atmospheric moisture, those unspent activators can start attacking all the metals in the system, the solder, component leads, and the PCB copper (see image).
Most liquid fluxes in use were formulated for use in selective and wave soldering, and capillary action is an important feature of fluxes in that capacity. However, the opposite is true on the rework bench where we need fluxes to stay close to the iron tip to minimize flux migrating under components where it may remain active and degrade reliability.
Our solder materials partner, AIM, recommends two types of specifically formulated flux for rework: NC280 liquid flux and NC217 gel flux. Both do not require exposure to heat to pass SIR testing. We primarily see liquid flux on the workbench, but for many rework applications, we recommend gel flux as it provides more controlled application than liquid flux, reduces spread, and cleans easier compared to other paste, tacky and even liquid fluxes.
So, the application should dictate whether liquid or gel flux should be used, and just as important is to make sure the rework flux used is specifically formulated for rework.